In the era of digital transformation and the development of innovative technologies, mobile laser scanning is emerging as a crucial tool across various industries. This cutting-edge method for acquiring high-precision spatial data revolutionizes information collection, optimizes workflows, and enhances operational efficiency.
Explore how mobile laser scanning can transform your business today.
Operating Principle of Mobile Laser Scanners
Mobile laser scanners utilize laser scanning technology to create three-dimensional images of the environment. They operate by measuring distances to surrounding objects using a laser rangefinder. A laser beam is directed at an object, and the reflected signal returns to the device, where it is converted into distance data. These measurements are performed in extremely short intervals, ensuring both high accuracy and rapid scanning speed.
One of the most advanced and promising types of scanning devices is the mobile laser scanner equipped with simultaneous localization and mapping (SLAM) technology. This innovation significantly enhances the scanner’s capabilities, making it an invaluable tool for a wide range of applications.
The SLAM Algorithm: Enhancing Precision and Detection
The SLAM (Simultaneous Localization and Mapping) algorithm utilizes distance sensors and data matching procedures to refine positioning and detect environmental changes.
The SLAM-based localization process involves two cycles:
- Prediction: Estimating future positions based on previous measurements.
- Update : Refining the local position estimate using new measurements.
Stages of the SLAM Algorithm
Each phase of the SLAM (Simultaneous Localization and Mapping) algorithm comprises the following stages:
- Receiving Measurements: Collecting data from sensors.
- Estimating Local Pose: Using the Kalman filter to refine current coordinates.
- Predicting the Next State: Estimating future positions based on movement.
- Map Matching: Identifying coinciding points between current and previous observations.
- Map Updating: Incorporating new dimensions into the map.
- Repetition: Transitioning back to step 1.
- Information Integration: Adding new data about the map and scanner positioning in each cycle to refine and supplement the map.
- Error Handling: If an overflow or error occurs, the matching process is terminated prematurely. It then returns to the map update cycle and repeats the entire algorithm.
As a result of the SLAM algorithm, a comprehensive map is created that reflects the location of all obstacles and objects, as well as the current position of the scanner.
Limitations of the SLAM Algorithm
The SLAM (Simultaneous Localization and Mapping) algorithm has several limitations:
- Processing Complexity: Handling measurements becomes complex, especially in environments with numerous similar terrain elements.
- Computing Resources: Creating a point cloud requires significant computing power.
Repeating Surfaces: Environments with repeating surfaces, such as long underground tunnels, pose challenges due to the lack of distinguishing elements. - Open or Narrow Spaces: Open spaces without distinguishing features or very narrow spaces can hinder accurate mapping.
However, combining scanner systems (GNSS, inertial, and SLAM) can effectively mitigate these limitations. Additionally, the success of mapping significantly depends on the expertise of the person performing the survey.
Advantages of Using Mobile Laser Scanners (MLS)
Mobile laser 3D scanners offer numerous advantages, making them an effective and sought-after technological solution for many production challenges:
- Automatic and Continuous Scanning: MLS allows for quick and accurate creation of digital models of objects or areas in the required coordinate system. Continuous scanning while moving provides a significant advantage over conventional terrestrial laser scanners, reducing data redundancy and increasing point cloud processing speed while requiring less computing power.
- Versatility: MLS can operate effectively both outdoors and indoors. In open areas, it utilizes GNSS receivers with geodetic accuracy and an inertial system. Indoors, the GNSS receiver is replaced by SLAM algorithms, ensuring continuous and accurate data collection.
- High Accuracy: Modern MLS provides precise distance and angle measurements between objects. Different classes of MLS offer varying degrees of accuracy, with some achieving millimeter-level precision (e.g., Trimble MX50) and others offering centimeter-level plan-height accuracy (e.g., Lixel L2).
- Integration with Various Devices: Mobile laser scanners can be integrated with various platforms, including cars, trains, scooters, briefcases, handheld setups, and drones. Manufacturers typically provide equipment sets to accommodate these different configurations.
- Cost and Time Efficiency: The use of mobile laser scanners reduces the time and cost associated with taking measurements, making them a cost-effective solution for a wide range of applications.
- User-Friendly Interface: Modern MLS devices feature intuitive interfaces, simplifying their use and making it easy to train new users.
These advantages make mobile laser scanners a powerful tool for efficient, accurate, and versatile data collection in various environments and applications.
Applications and Use Cases of Mobile Laser Scanning
Mobile laser scanning technology is highly versatile and can be used across various industries, including engineering, geodetic surveys, urban planning, construction, manufacturing, and more.
Engineering and Geodetic Surveys, Urban Planning:
- Urban Area Surveys and Mapping: Mobile laser scanners can quickly and efficiently gather detailed information about terrain, land use, infrastructure, and other urban elements.
- Construction: Construction Monitoring: Scanning technology allows for monitoring the compliance of construction projects with design documentation, identifying deviations, and making timely adjustments.
- Road Work: Mobile laser scanning is used in road construction in three main areas:
- Engineering and Geodetic Surveys: During both design and as-built surveying phases.
- Certification and Inventory: Of existing infrastructure.
- GIS and Geospatial Databases: Creating geographic information systems and databases for roads.
- Ecology: Environmental Monitoring and Forest Management: Accurate Forest mapping for forest management, restoration planning, and logging control.
- Mining Industry: Surveying Efficiency: Mobile laser scanners can significantly speed up surveying processes, reducing team sizes from four or five to one or two people. This technology is already in use in many mining enterprises, such as the Polar Branch of PAO Norilsk Nickel, where measuring a 100-meter mine opening with a mobile scanner takes about three minutes, which is 40 times faster than traditional methods.
Key applications in the mining industry include:
- Surveying unique natural underground objects.
- Inspecting underground storage facilities (oil, gas, hazardous nuclear waste).
- Generating complete three-dimensional models of mine networks.
- Controlling the stability of quarry sides or open pits.
- Accurately assessing the broken ore mass.
- Examining local rock falls or collapses to develop re-strengthening documentation.
- Assessing the dynamics of destroyed rock volumes in boundary coal-rock massifs during periodic inspections.
- Significantly reducing the labor intensity of surveying.
Mobile laser scanning offers a powerful and efficient solution for a wide range of applications, driving innovation and improving processes across multiple industries.
Examples of Mobile Laser Scanning Use
Example 1: Office Premises and Parking Lot
We conducted a scan of an office building and its parking lot using a Lixel L2 mobile laser scanner. The scanning was performed in the “Indoor” mode, designed for indoor or narrow spaces. The Lixel L2 scanner also features two other modes:
- Outdoor: For open spaces.
- Semi-outdoor: A mixed scanning mode ideal for street surveying.
The accuracy of the SLAM algorithm and the resulting point cloud construction depend on selecting the appropriate scanning mode. This scanner has consistently delivered excellent results across all surveying scenarios.
Pure Surveying Example: Office Premises and Parking Lot
The surveying was completed in a single pass, taking no more than 30 minutes in total. The process began inside the office premises, continued down the stairs to the parking lot, made a full circuit along the parking lot’s perimeter, and then returned to the starting point.
During the survey, there were several challenging areas for constructing point clouds using SLAM algorithms, such as narrow office corridors and stairs. The scanner performed exceptionally well, with no noticeable geometry distortions in the resulting point cloud.
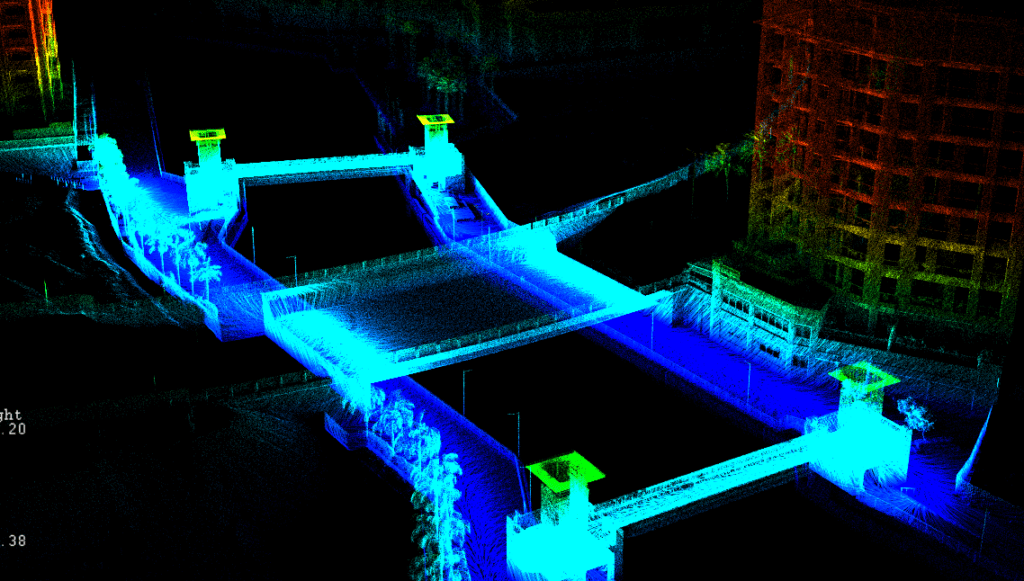
Pure Surveying in Mixed Conditions:
Surveying in Mixed Scanning Mode
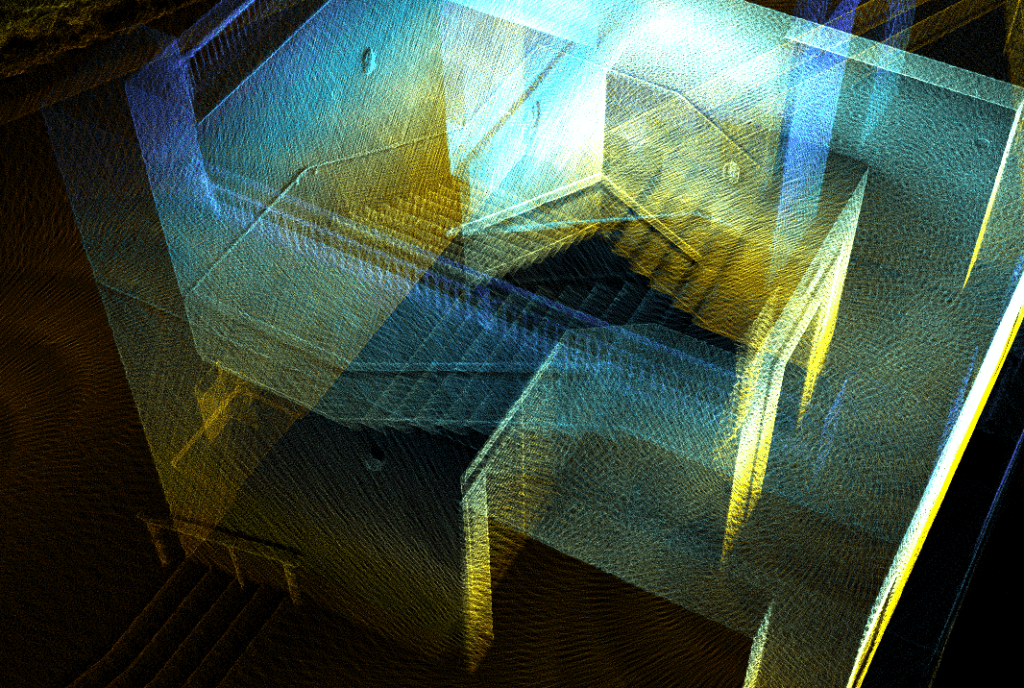
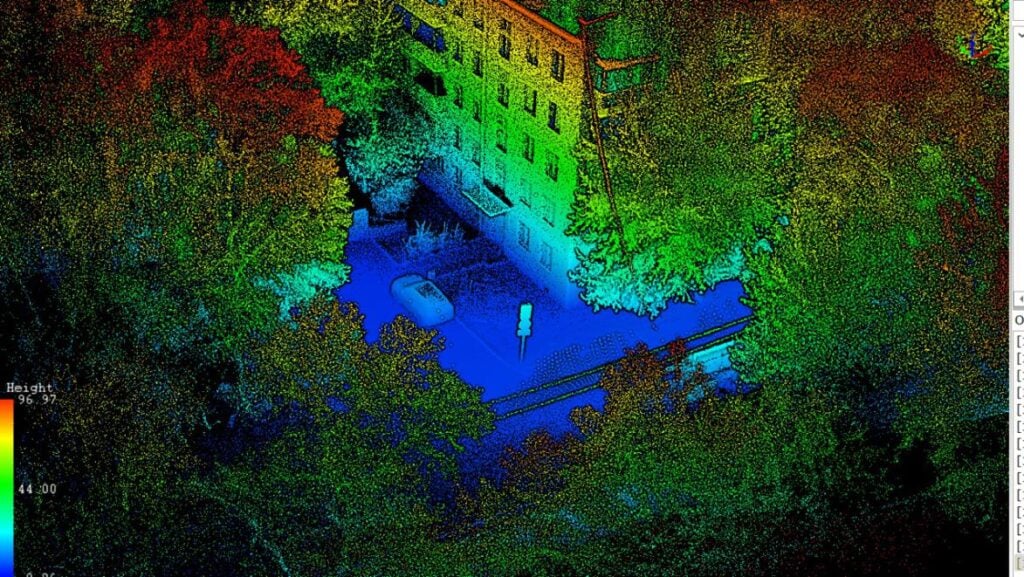
Unique Feature of the Lixel L2 Laser Scanner
A notable aspect of the Lixel L2 laser scanner is its ability to generate a cloud of laser scanning points in real-time during the shooting process. This cloud is created in las format and has a density approximately 25% of the point cloud obtained after raw scan data processing (see Fig. 7).
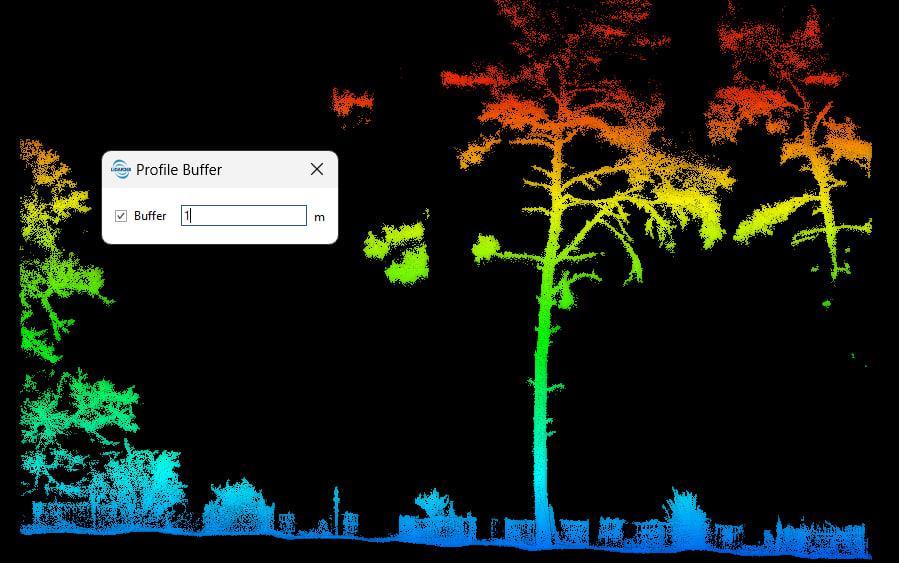